REDUCE HUMAN PRESENCE
CONTROL OPERATON, MONITOR TRENDS AND ANALYZE DATA FROM ANYWHERE
FIVE REASONS TO AUTOMATE
- SAVE COSTS AND RESOURCES
- INCREASE QUALITY & REDUCE RISK
- INTEGRATION RELEASES RESOURCES
- UTILIZE DATA TO ACHIEVE FURTHER INCREASED EFFICIENCY
- LESS CLIMATE IMPACT
First; SAVE COSTS AND RESOURCES
Using the internet, our application of standardized and open technologies allows secure real time control and monitoring of a worldwide activity. Moving operations from local to remote, with a common control center, can lead to a significant reduction in costs and footprint without having to make significant investments:
- Control without actual presence
- Monitoring without actual presence
- Updates without actual presence
- Faultfinding without actual presence
It also provides the ability to collect and compare real time process data from multiple plants at different locations. Additionally, a basis for a significantly increased quality of performance is established.
A basis is established for replacing local presence with remote control from a global control center
Second; INCREASE QUALITY & REDUCE RISK
By integrating the correct range of instrumentation, sensors and control logic, the machinery can be transformed from an assorted collection of devices that requires individual attention, to semi-autonomous system that independently collects sensor data and reacts quickly and correctly to situations that arise within the process.
This implies every operation identically performed:
- The optimal measure is taken by the algorithm
- The automated sequences can include self-tests to assess the state of the machinery. Thus, maintenance can be performed as needed instead of by a fixed schedule
In autumn 2020, we performed the first upgrade that included self-directed sequences, of an existing process plant control system (original installed in 2014). The intention was to transfer the control and monitoring from offshore to an onshore location. The first job performed remotely from shore was completed as planned and with negligible human input. As the PLC program is installed locally, the processes will not be affected by any interruptions in communication between offshore and shore. If a command is given and received, the automated process will be carried out to completion. In the future, we expect opportunities for similar assignments to present themselves.
To transform the device from simpleminded to a robot implies a significant increase in quality and performance
System integration is the process of bringing together subsystems into one common system and ensuring that they function together as a whole. The common practice here revolves around achieving shorth-term ad-hoc objectives by creating point-to-point links between subsystems. This allows systems to grow quickly in complexity and is unsustainable long-term. Barriers to integration are maintained and significant potential gains remain untapped.
- One team of operators control all connected systems
- Free exchange of data as all systems speak the same language
- Improved information flow provides a deeper understanding of process status and improved basis for making decisions
- All systems monitored through a common communication network, avoiding collections of separate monitors and networks
- Full flexibility with plug-and-play replacement of components
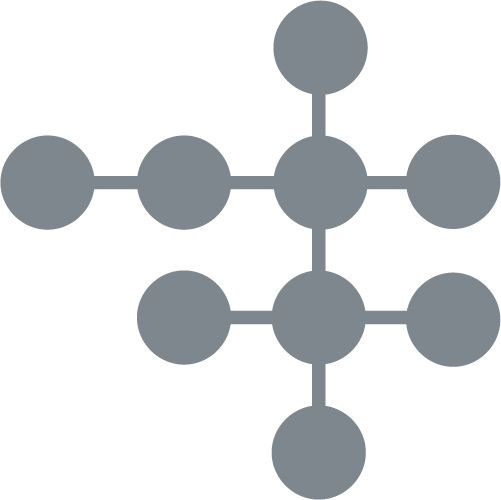
Several process controlled from the same HMI monitor
Fourth; UTILIZE DATA TO FURTHER INCREASE EFFICIENCY
The control system collects a large quantity of data which, through structuring and analysis, can make a significant contribution to further increased efficiency and quality. It may be input to:
- Condition based maintenance
- Input for continuous improvements
- Data transfer to surrounding processes
- Manufacturing Execution System (MES)
- Enterprise Resource Planning System (ERP)
- Machine Learning
Our use of standardized and open technologies simplifies your data analysis. The logging & trending solution is an integrated part of our control system and is available via the internet, with no need for an additional application or plug-ins. To ensure the required level of security, a complete model that includes application security, transport security, user authorization & authentication, and traceability is available. This enables full access to the Log & Trend data via internet.
Analysis and structuring of process metrics to accommodate data-driven improvements
Fifth; LESS CLIMATE IMPACT
Our solution provides increased sustainable economic activity which will have a substantial positive impact on the climate and the environment:
- By remote access via internet, presence is achieved without the resource consumption involved in movement, transport and accommodation for on-site personnel
- By continuous development of automated sequences through lessons learned / best practices, tasks will be performed with ever less resource usage, including reduced emissions and waste to the surrounding environment
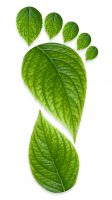