Complete software package for full control
and all information from anywhere
We are building software modules that cover everything you would expect from a control system for process plants – both today and in the future. These all build upon our Connect it framework that facilitates control and monitoring via the internet using standardized and open technologies.
Once the foundations are in place, the scope of the control system can be expanded with modules for robotization, reporting, remote support, condition-based maintenance and simulation. Every new addition integrates seamlessly within the same infrastructure thanks to our future-minded approach. All that is required for full plant control and data access is a browser, a monitor, and credentials
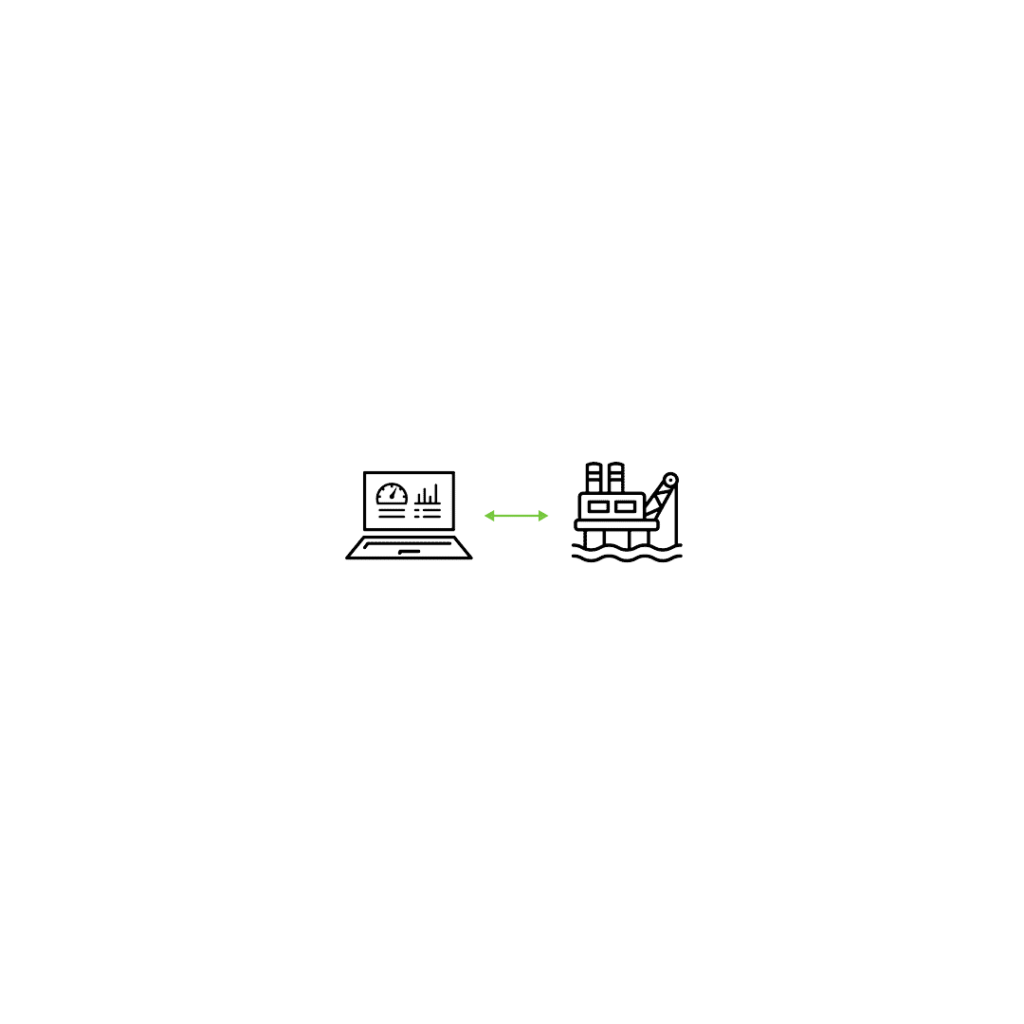
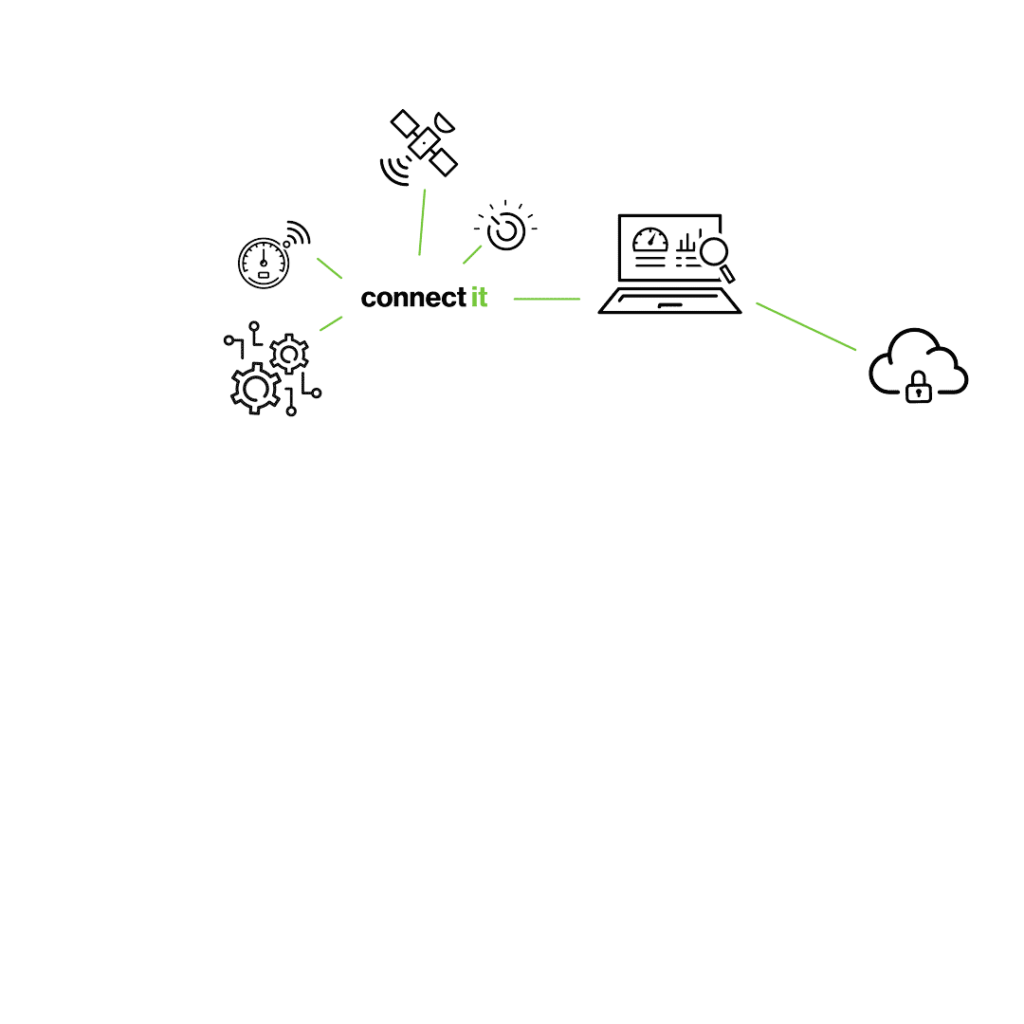
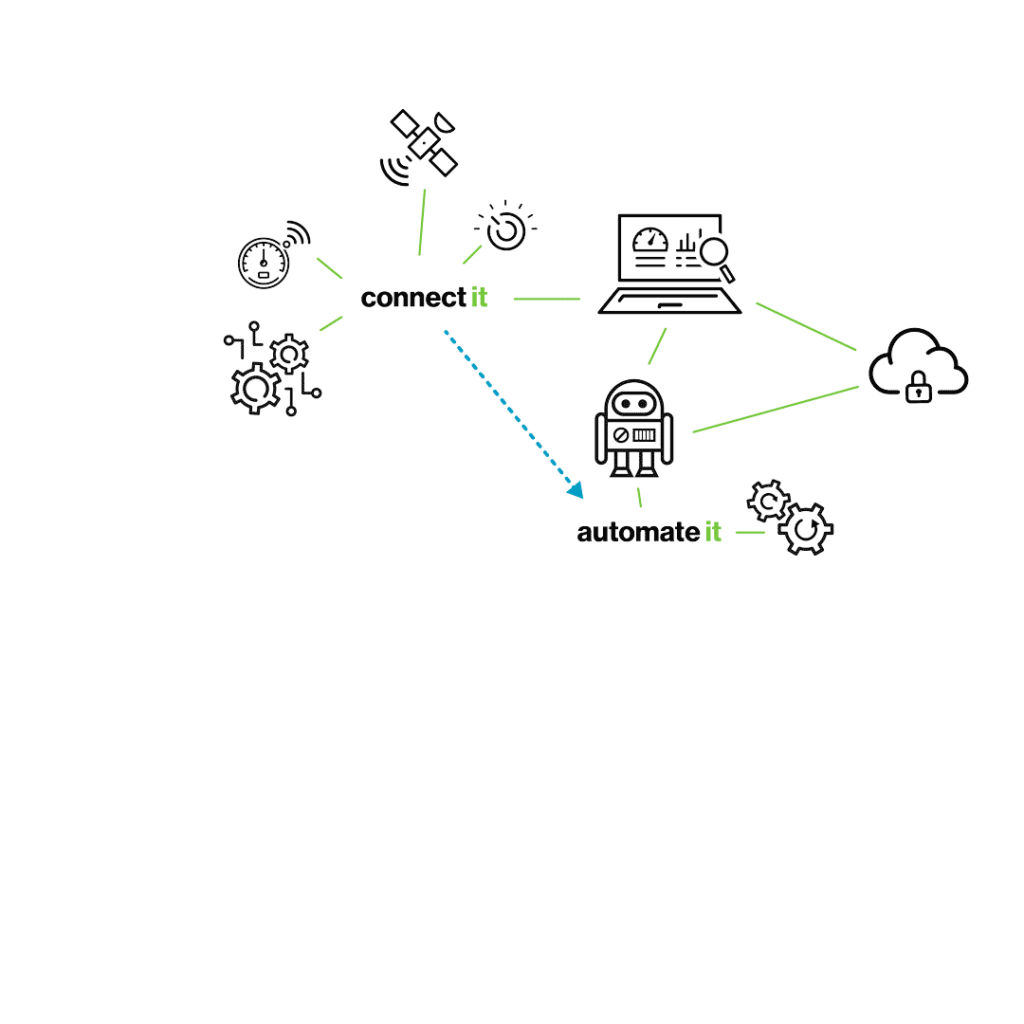
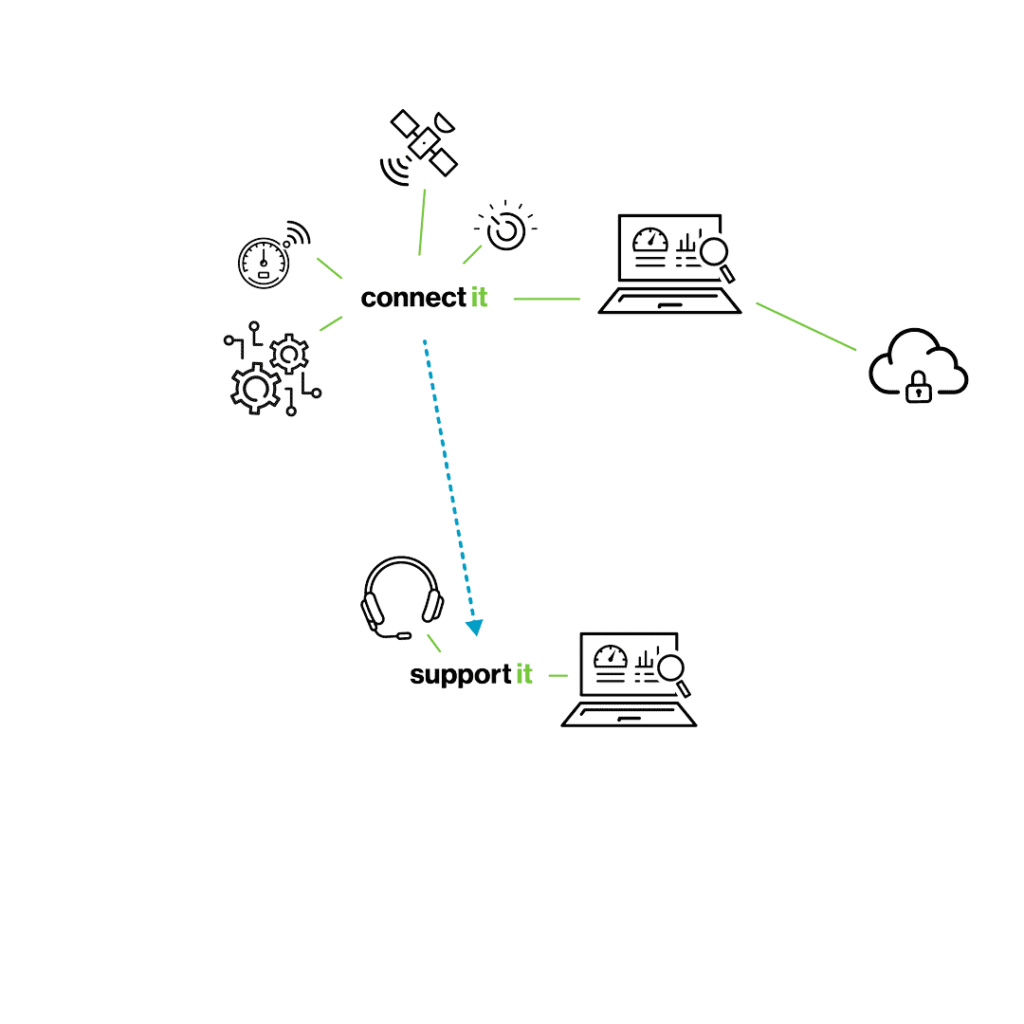
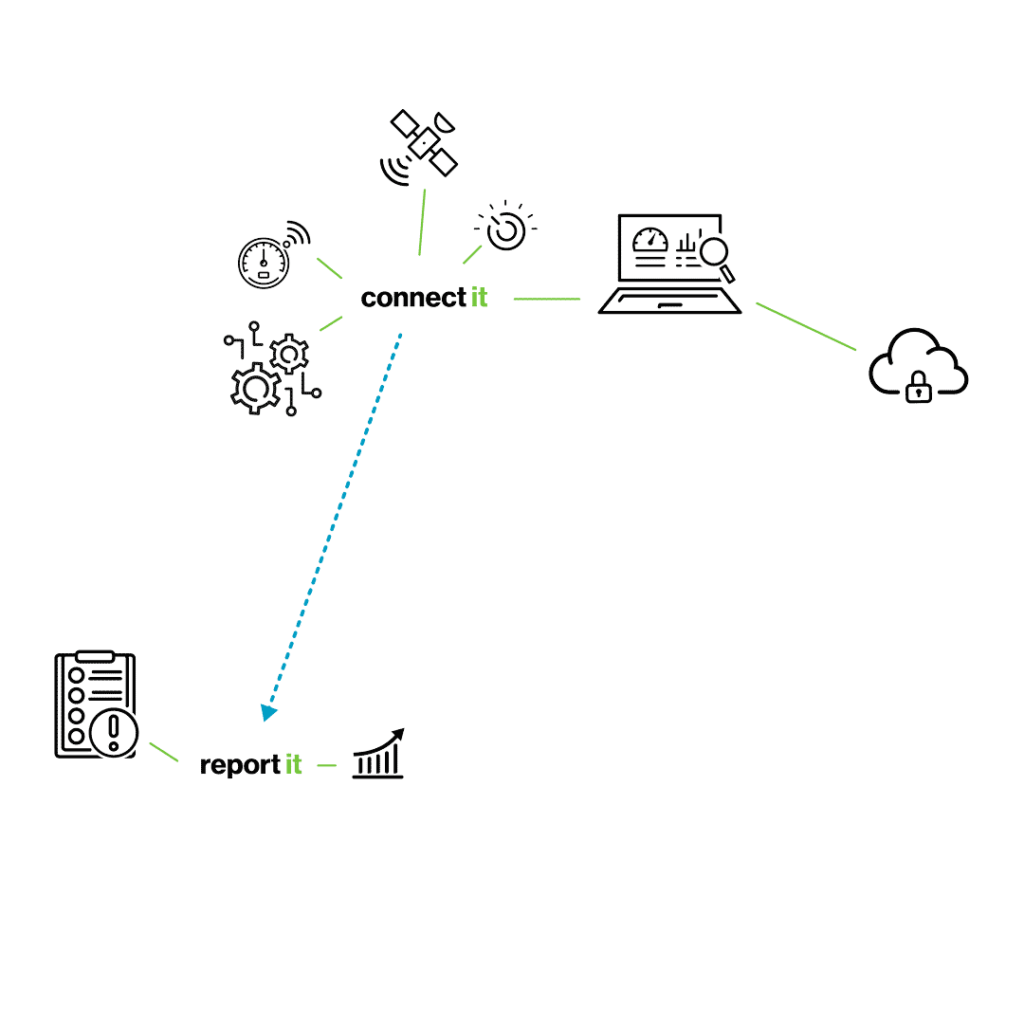
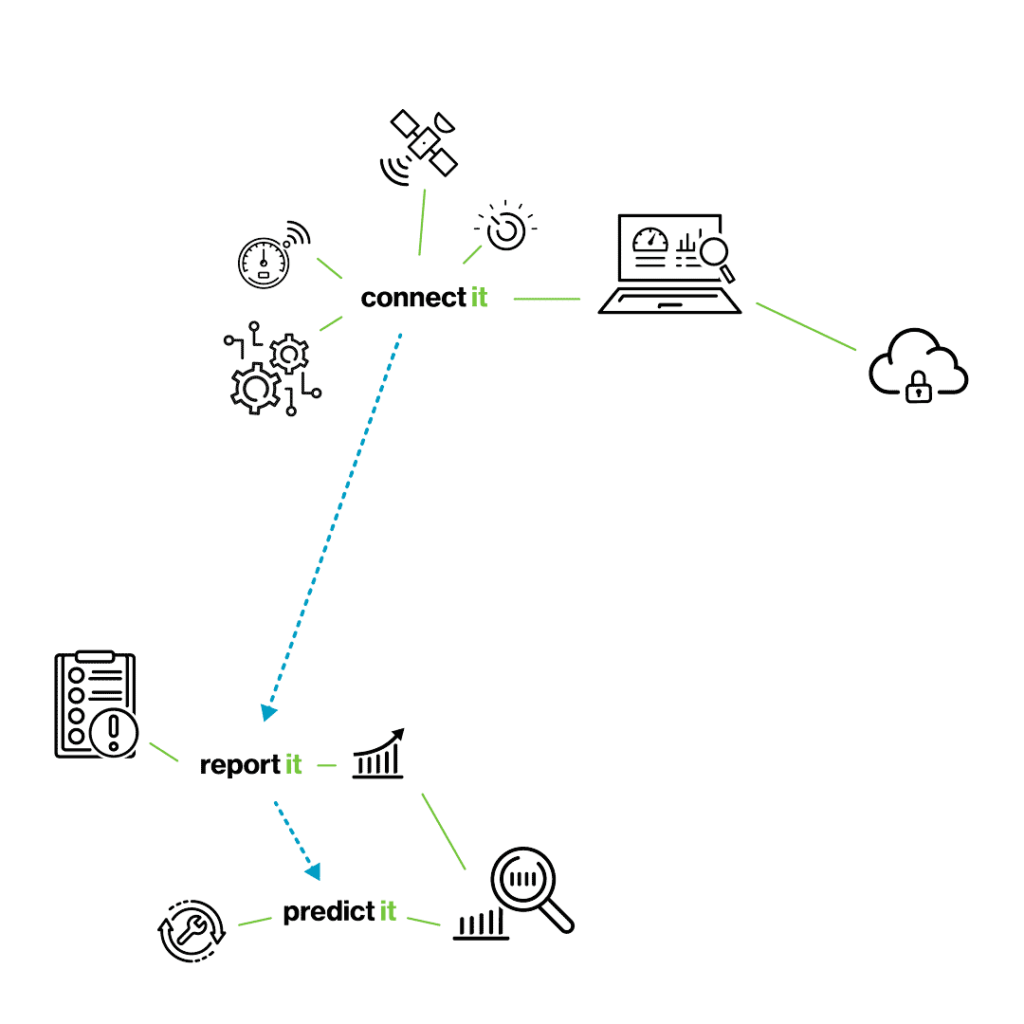
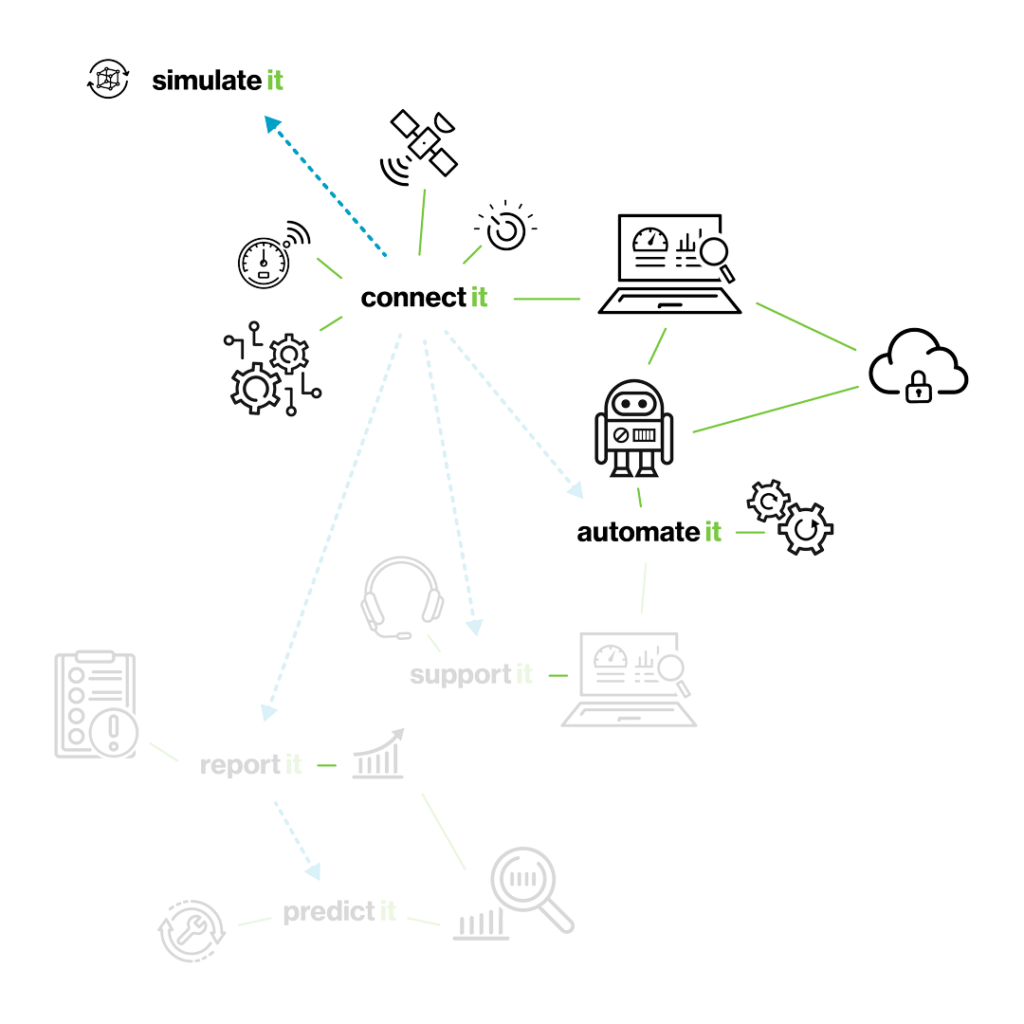
connect it
Get connected
Lay the foundations for remote control. Connect hardware and software, and bring your system online.
automate it
Robots do not make mistakes
Boost quality, efficiency, and safety with automated sequences to manage the details of the process. The operator keeps their overview, while the robot is there to assist.
report it
See all, know all
Live trends and historical data, directly integrated into the control system and accessible from anywhere.
support it
Stay connected
Receive live support and troubleshooting when needed, and software updates when available. Less waiting, less trouble, less downtime.
predict it
Two steps ahead
Monitor equipment conditions and process parameters to improve efficiencies and reschedule maintenance to when it is actually needed.
simulate it
Try this on for size
Test and train on a digital twin of the plant to simulate operational changes, prepare new operators, and to link the end-user into the design loop.
Description of the software modules in detail:
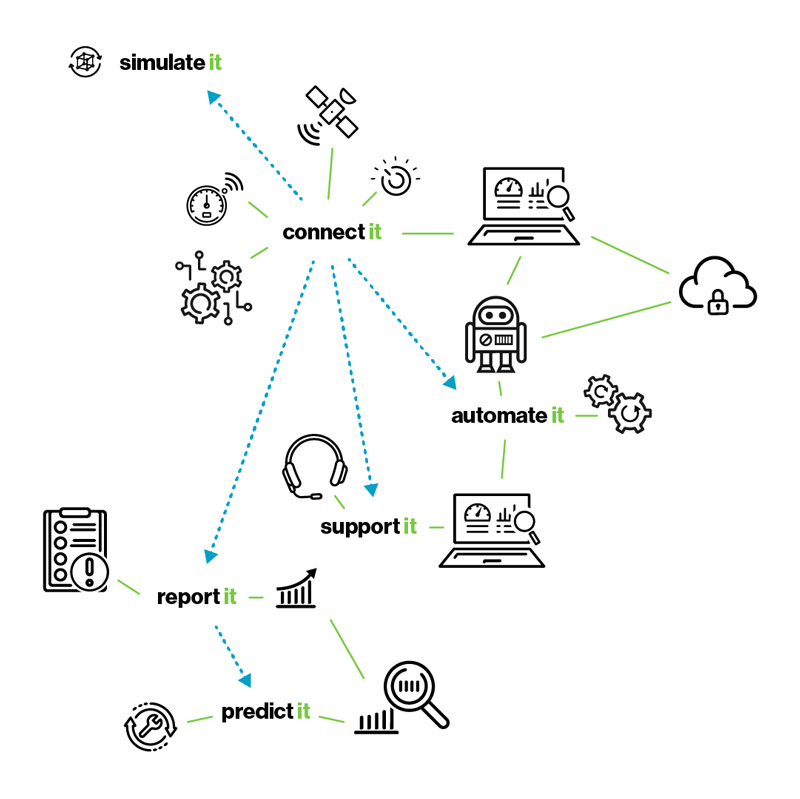
connect it
Get connected
automate it
Robots do not make mistakes
Expand the basic remote-control system with the Automate it software module to gain the benefits of sequential programming. By stitching together commands we give the operator access to pre-programmed routines while they keep their focus on the bigger picture. Condition-checks and regulators handle deviation cases while notifying the operator of the event. Minimize incident chances and make sure operations run correctly each day!
- Less reliance on human factors means fewer mistakes that impact operations.
- Better repeatability means a more reliable product quality.
- Computers multi-task better and react faster than their human counterpart, leading to savings in time and power consumption.
- If the operator loses connection to the plant, the controller can still complete vital tasks and shut down safely, as all logic is processed locally.
- The operator can keep a full overview over the condition of the plant, while the controller takes care of the operational details.